GI Joe: The Evolution Of An Action Figure
Exclusive! How Hasbro turn movie stars into plastic poseables...
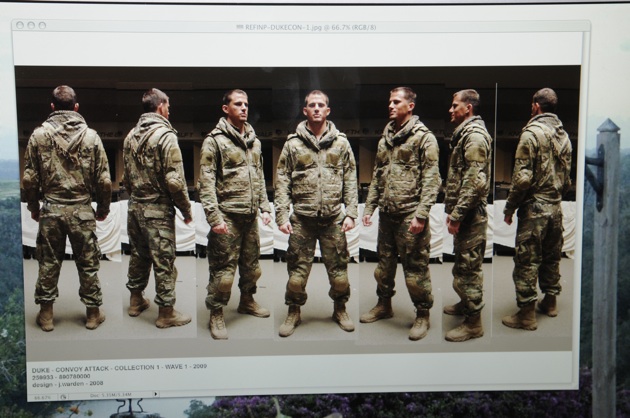
No Ordinary Joes
The days when action figures looked less like the actors in the movie and more like freshly shaven monkeys are long gone.
When Hasbro started preparing to make their movie tie-in GI Joe figures, they dispatched a team to Hollywood. Their job? To photograph the actors in costume, but most importantly to scan their heads using a gizmo that creates a 3D, 360-degree image of each actor's head.
“They basically stand in a dark booth while this thing rotates around them,” says design director Michelino Paolino, who pulled rank to make sure he got the gig. “Yeah, going on set to do that was one of my duties,” he grins. “Scanning Sienna Miller, Rachel Nichols, Karolina Kurkova... Those are tough days.”
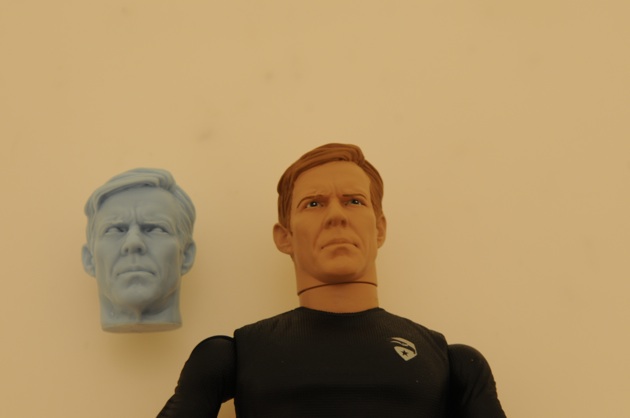
Heads Up!
The 3D scans are then run through a stereo lithography machine. A stereo what-now? Well, just think of it as a 3D printer that layers and shapes resin into an exact real-world model of the star's head.
Those model heads still go back to the stars for approval, but they're so accurate they can't really complain too much. “Dennis Quaid can't say to me, 'Well, my ears look all floppy!'” says model shop boss Marc Millspaugh. "Because I can say to him, 'Well, dude, that's because your ears are all floppy!'”
There were virtually no problems on GI Joe though – the stars, especially the boys, loved the idea of being turned into toys. “Channing Tatum was, like, 'I'm an action figure! Kids are going to be playing with me!'” says Michelino Paolino. “Marlon Wayans who plays Rip Cord was the most excited, though. I don't think any of his brothers have got action figures yet.”
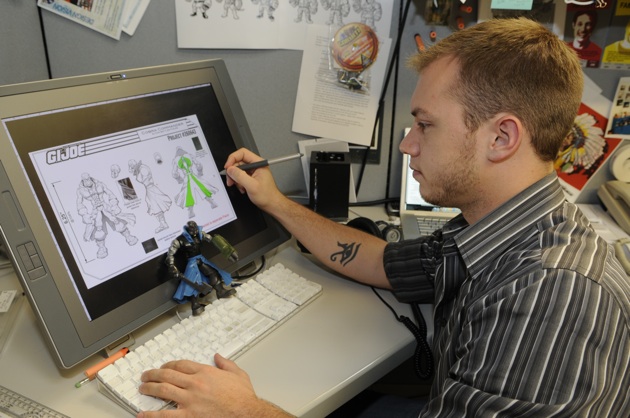
Etch-A-Sketch
While the heads are being made, the multiple body shots are turned into a 360-degree artist's impression. This could be done via a scanner too, but splitting the two methods has advantages.
First, stars only need to be given approval on their faces, not bodies: requests for biceps to be bigger or bums to be smaller can be ignored. Second, Hasbro's designers need the freedom to tweak the bodies a bit more. They need to move packs, pockets and boot tops around so they can cleanly fit in all 16 points of articulation (joints, basically) that the three-and-a-quarter-inch figures need so they can be posed.
They take this very seriously. Nobody laughs, for instance, when Total Film suggests that 16 points of articulation is more than most real-world action stars can muster...
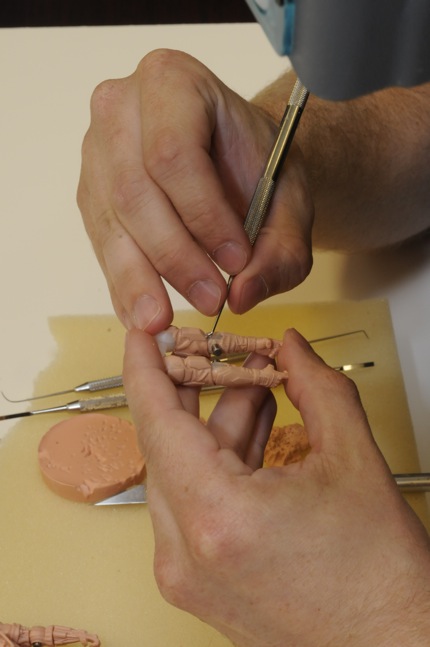
Wax On/Wax Off
There's something pleasingly old school about the way the physical body of an action figure gets made.
The designers basically take a plastic articulated 'skeleton', coat it in wax. and then one of the sculpting team manually carves out all the detail to match the artist's sketch design for the body.
It's painstaking work that requires a steady hand, big magnifying goggles and an array of pointy tools that look like Laurence Olivier's dental torture kit from Marathon Man .
“It usually takes about three weeks to do a complete figure, scratching out all the folds and belt buckles and so on,” says Michelino Paolino. “And they're very, very fragile!”
( Total Film shamefacedly snatches back the hand that was about to pick one up...)
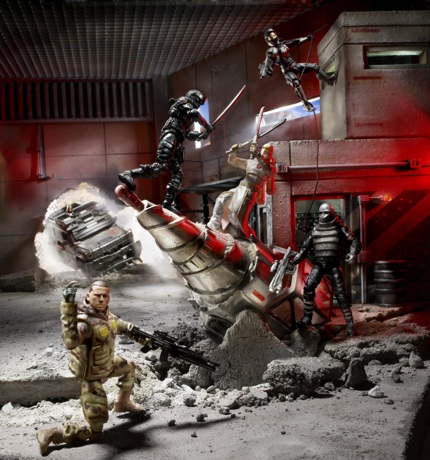
New Model Army
Once the wax figure is carved to perfection, a mould is cast from it and a hard plastic copy is made.
That's the version that's sent off to a factory in Hong Kong to be used as a template. (As with most typically American things, the figures aren't made in the US).
Once the production lines get going, that single figure could be turned into anything from a few thousand identical copies to up to 5 million. And sometimes even that isn't enough...
“I had one actor – and no, I won't tell you who it was! - call me up once and ask for 500 of his action figures for a family reunion in Alabama he was having,” says Marketing Director Michael Ritchie. “I gulped. I only had about seven in my office...”